Hello everyone!
This is a little 3D Printed project of mine I finished a few weeks ago for my new Sam Yang Recluse .357 cal Air Rifle.
This is a long post, with lots of pictures. Share, like, subscribe, comment if you like it and thumbs down dislike if you hate it.
If you are familiar with the other Korean Sam Yang big bore air rifles like the .457 cal 909 Light Hunter or the big one the .50 cal Dragon Claw you know that these types of PCP air rifles are a bit on the heavy side.
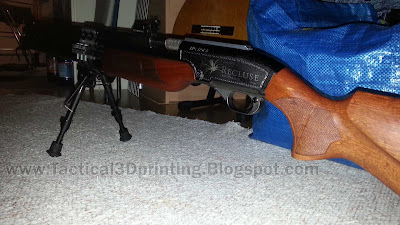 |
Sam Yang 357 Recluse 2016 - 3D Printed Barrel Bipod Mount |
Especially now since they have come out with the 500cc dual-tank models. The .357 Recluse weights in at
8.5 lbs. While the more compact and small caliber .22 and .25 cal Sam Yang Sumatra Carbine weights in at around 6 lbs. Sure it's not that heavy but I like to sit down and shoot mine from a rest and also do some free hand shooting.
So I figured I'll just slap on a swivel bipod and be done with it, however due to the design of the Sam Yang air rifles I found that for my taste the bipod came a little bit too far back.
And also it made it difficult to do free hand shooting with having the swivel bipod mounted in that location seen here in this picture.
Now that picture show you the old single-tank model of the Dragon Claw and that could work just fine. But I also found that with the new 500cc dual-tube versions they are more heavy in the front. So often if I wasn't careful when I picked up mine it would just tip over and bang the tube in the floor.. Too much weight in the front and the bipod located too far back to balance the rifle.
Well what do you have a 3D printer for if not to fix things right!
So I needed to mount the bipod to the barrel, however being an air rifle and also a dual-tank PCP air rifle there isn't really any bipods that allow you to do that with this setup. I figured I needed to make something strong that would hold some abuse, and also be slim enough that I still could use the iron sight on the rifle if needed.
Luckily the iron sights on the Sam Yang air rifles are mounted very high of the barrel so having something mounted around the barrel would not distract or block the sight. Another thing was I didn't want to pull anything apart from the rifle when mounting the bipod, and if the mount should brake it needed to be able to come off with ease.
Off to Solidworks and do some CAD Design!
 |
Sam Yang 357 Barrel Bipod Mount v5 top Solidworks CAD |
So the first thing I do when 3D printing is determine the exact dimensions. And what I mean by that is in this case I wanted the top part seen in the picture to have a tight fit to the barrel and snap into place when fitting. There needed to be enough strength to the part that it would not brake in use, but also be flexible enough to be able to go over the tubes. The design seen here is version number 5.
3D printing is not an easy thing, really. It's just like any form of practice, it's an art and it takes some time to master 3D printing. These air rifle parts needed to be strong so ABS plastic is what needs to be used, if not then Nylon is the preferred material. Both materials have different properties and uses and they also print different.
To get the right tolerances on the top part I designed 5 parts and printed 3 of them to check if they where fitting like they should on the barrel. Now I didn't finish the prints because I only needed the outline of the barrel printed, and that took only a few layers to get, so once I was happy with how it looked and tweaked the design I went ahead and printed the final fifth version and it snapped on just like I planned.
 |
Sam Yang 357 Barrel Bipod Mount v5 bottom Solidworks CAD |
The bottom tube is the big one and this is the part that needed to both snap on and fit snug to the tube and attach to the top part. And also finally attach to the swivel bipod.
I made the decision to attach the bipod to the bottom with the same configuration swivel type stud and I figured it would hold if I printed this in one piece.
 |
Sam Yang 357 Barrel Bipod Mount v5 Assembly Solidworks CAD |
This is the final assembly in Solidworks and you can see that the holes line right up, because I measured twice! I made the holes on the top part big enough that I could fit some 5mm bolts I had, and the holes in the bottom part I made smaller so I could use a thread tap. This way I didn't need to use any nuts and the ABS plastic is plenty strong to hold threads.
 |
Sam Yang 357 Barrel Bipod Mount v5 Assembly Side Solidworks CAD |
However I went ahead and added some space to fit nuts if it so happened that the threads in the plastic would fail sometime in the future.. Or if I messed up the delicate procedure of tapping plastic!
Here it is! Finally 3D Printed Bipod Mount!
 |
Sam Yang 357 Recluse 2016 - 3D Printed Barrel Bipod Mount v5 2 |
Well I didn't mess anything up, and what it looked like on the computer is how it turned out in real life also! And I managed to tap the threads in the holes without problems for the 5mm bolts that are holding it together.
 |
Sam Yang 357 Recluse 2016 - 3D Printed Barrel Bipod Mount v5 1 |
Looks nice does it not, both parts fits nice and snapped over the barrel and tubes. So there is no need to take anything off the rifle to remove the mount. Well I could probably have only used 4 bolts to hold things in place, and not the 6 bolts like how it was designed to begin with. However I like to think that 6 bolts spreads the load a bit more even over the barrel and tubes so it's less a strain on the ABS plastic that way.
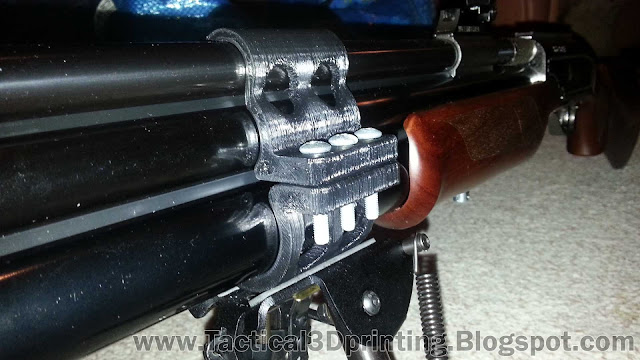 |
Sam Yang 357 Recluse 2016 - 3D Printed Barrel Bipod Mount v5 3 |
Now for you that already have been 3D printing for a while and want some details, these two parts where printed separately. I didn't use any support material on the parts to print these. And I often design and print parts so I don't need to use any support material because it always takes some time to remove afterwards.
I find it that if I can make a part without support material it turns out looking cleaner.
 |
Sam Yang 357 Recluse 2016 - 3D Printed Barrel Bipod Mount v5 4 |
You might notice that the bolts used are a bit on the longer side, almost twice the length needed. But at the time these where the bolts I had handy at the time, and I guess I could shorten them.. But it just takes so much time to screw these in and out by hand, the thread pitch is 0.75mm!
 |
Sam Yang 357 Recluse 2016 - 3D Printed Barrel Bipod Mount v5 5 |
This Sam Yang Recluse is not front heavy anymore! Now I can pick it up and not have to worry about it tipping over. And I can do free hand shooting too without having the bipod in the way!
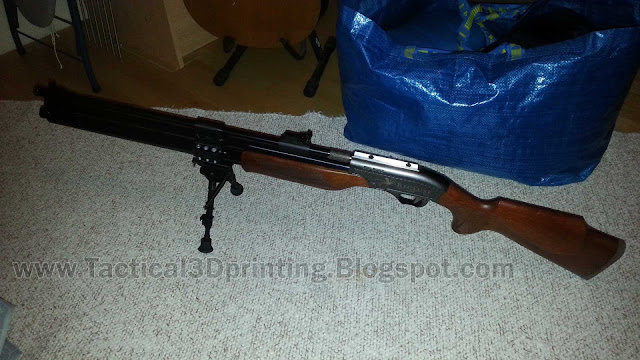 |
Sam Yang 357 Recluse 2016 - 3D Printed Barrel Bipod Mount v5 8 |
The bipod mount is also slim enough over the barrel that it won't get in the way of the iron sights when aiming down the sight. And you would need to have a really big scope on there to even get close to it. But the thing is, I can also slide the bipod mount all the way to the front if I ever needed to. Just slightly undo the 6 bolts and the bipod and mount slides back and forth.
 |
Sam Yang 357 Recluse 2016 - 3D Printed Barrel Bipod Mount v5 6 |
Ok so, to get back to the 3D printing settings I used. The 3D Printer is the Rostock Max running ramps hardware custom 3D printed bracket for extruder heat shield that is used when printing ABS and cooling fans to keep temperature under control. Cura is my preferred slicer.
EZstruder is a direct drive extruder and for me to get good retraction on the prints I run around 800mm/s and 10-12mm for ABS with the stock Rostock Max 0.5mm nozzle. Remember this is a direct drive extruder, so you need to run the extruder stepper motor faster and longer than a geared one. But not too fast or you start to grind the filament. And make sure you run cooling fans on the board or the extruder stepper motor will start to skip and loose steps.
I think I used 0.30mm layer height on this 3D print, and 90% infill. I usually need 30 brim lines to make sure the part sticks to the bed good. I find that 0.30mm layer height gives decent looking 3D prints and it also more importantly cuts down on the overall print time. However for smaller parts I normally do 0.15mm if I need that extra detail. Extruder temp around 220c and bed temp around 70c. The bed I use is a mirror on top of a machined 5mm aluminium plate that's sitting on the Rostock heater platform. To get parts to stick good to a mirror or glas surface I personally use wood glue that's diluted with water. A few coats on the mirror and the parts stick well, however it is critical to have the right height on the first layer. Even 0.05mm difference here is what can cause the print not to stick good on the bed and you start to get corners lifting or the whole part coming loose. I find that for me I get better finish if I only run around 45mm/s for the inner and outer shell speed and I found that the black Chinese ABS plastic I have right now didn't like anything over 65mm/s on the infill or it would start to make holes in the infill.
Print time for both parts I estimated to around 2-3 Hours, but I printed one part at a time and also did some design while the parts where printing so not to bad. But there is not really anything you can do about the print time. If you want the print to look nice and not fail mid way etc. It's always best to stay with what you know works and not try and rush things.
 |
Sam Yang 357 Recluse 2016 - 3D Printed Barrel Bipod Mount v5 7 |
So in the end I probably ended up spending a week on the design and printing, I recon about 10 hours to get to this point with the bipod mount. Did I mention it broke? Well it did, I attached the bipod and started to tighten the screw for the swivel stud and it broke the little hole on the bottom of the part. That plastic part that supposed to do the job of the swivel stud and hold the bipod in place.
On closer examination I found that the bottom printed part was a bit to large for it to go down into the hole in the bipod. So I had to carve out a bit on the sides of the "plastic swivel stud" so that it would fit and then it all worked like it should.. But it's nothing like it when you spend hours printing something and it starts to brake before you even get it assembled.. But it turned out OK this time.
So if there is anything that I would think would brake on this 3D printed bipod mount then it's that little plastic swivel stud. So in the future if that happens I might just make a new bottom part with the plastic swivel stud replaced with a real swivel stud and have that threaded into the plastic instead. Oh and I might just shorten the bolts while I'm at it.
Thanks, Share, like, subscribe, comment if you like it and thumbs down, dislike if you hate it.
UPDATE: New Bipod Barrel Mount Part Fixed
 |
This is the updated bottom part for the bipod that I made as a quick fix |
◙ UPDATE: 3D Printing a Sam Yang Recluse .357 Bipod Barrel Mount ◙
You may also like
◙ 3D Printing a Rifle Stabilizer ◙
Do you have a steady hand?
No comments:
Post a Comment